压力淬火是一种专门在热处理时用于减少复杂形状工件变形的淬火工艺。工业热处理操作中出现的变形是由很多的独立因素引起的。其中一些因素包括:制造工件的材料的质量和之前的加工历史;工件残余应力分布和先前的热处理历史;淬火操作本身引起的非平衡的热应力和相变应力。由于这些因素,高精密工件(如工业轴承套圈和汽车螺旋锥齿轮)在无约束或自由油淬时经常会出现不可预见的变形。
压力淬火是以一种精心控制的方式,使用专门的工具,产生束缚工件运动的集中力,有助于使这些工件的变形最小化。如果操作得当,这种淬火方法通常可以实现工业制造规范中所规定的相对严格的尺寸要求。它通常用在由铁基合金和非铁基合金制造的各种复杂工件中。使用压力淬火的普通钢合金通常包括高碳透淬钢(如AISI52100和A2工具钢)和低碳渗碳钢(如AISI, 8620和9310) 。
渗碳钢尤其可以从压力淬火的过程中受益,原因是其加工性质及其在汽车行业以及工业及消费产品的齿轮传动装置中的普及性。理想的情况是,淬火期间,工件整个横截面上的转变温度是一致的,以便能够均匀地发生转变。然而在渗碳工件中,马氏体转变温度在整个横截面上并不一致。在渗碳过程中,扩散到零件表面的碳产生了一种成分梯度,导致表面附近的转变温度也呈梯度形式分布。在淬火期间,这一梯度将会促进或恶化这类工件的变形问题。基体材料显微组织的非均匀性(如严重偏析材料)也会导致这种类型的变形。一般情况下,与厚且重的几何结构紧凑的零件相比,大孔径轴承套圈之类的大型薄壁零件更容易受到这些变形问题相关因素的影响。虽然压力淬火不能消除这些影响,但它的使用有助于使这类变形问题最小化。
热处理过程中所产生变形的严重程度强烈依赖于工件所采用的热处理过程的本质。为了使淬火过程的变形最小化,零件的散热应该尽可能均匀。在几何形状有突然变化的情况下,这一点将很难实现。例如,在同一个零件中,薄断面与厚断面相邻。一个很好的例子是大齿轮或小齿轮上的齿。与大齿轮和小齿轮体相比,齿的表面积与体积比更大,在淬火期间,它们通过“展成”有变形的倾向。虽然这类零件在自由淬火或无约束淬火时会产生不可预期的变形,但是轮齿这种特有的运动在压力淬火操作中重复性很好,从而可以在齿轮设计时加以考虑,以使淬火后的磨削量最小化。随着工件浸入淬火冷却介质中,轮齿将比邻近的较厚部分更快速地冷却和收缩。这种冷却速率不同造成的结果是,当工件的其余部分仍处在胀大状态时,较薄较轻的部分趋向于迅速硬化和收缩。因为较厚的部分以一个相对缓慢的速率冷却和收缩,在薄厚相连的地方,其相对运动会受到阻碍。结果就是薄截面比厚截面转变
得更加快速,导致出现了温度梯度和不均匀的组织应力。在压力淬火时,通过选择性地引导淬火冷却介质流向较厚的部分,同时远离较薄的部分,以促进淬火更均匀来解决这一问题。这一措施主要是迪过使用专门的工具来实现的。通过采用这一重要的措施,可以使由转变引起的变形很小。

在20世纪30年代初,淬火机床开始广泛应用于美国的工业生产,主要用于汽车(包括轿车和卡车)环齿轮的加工(图 1 ) 。
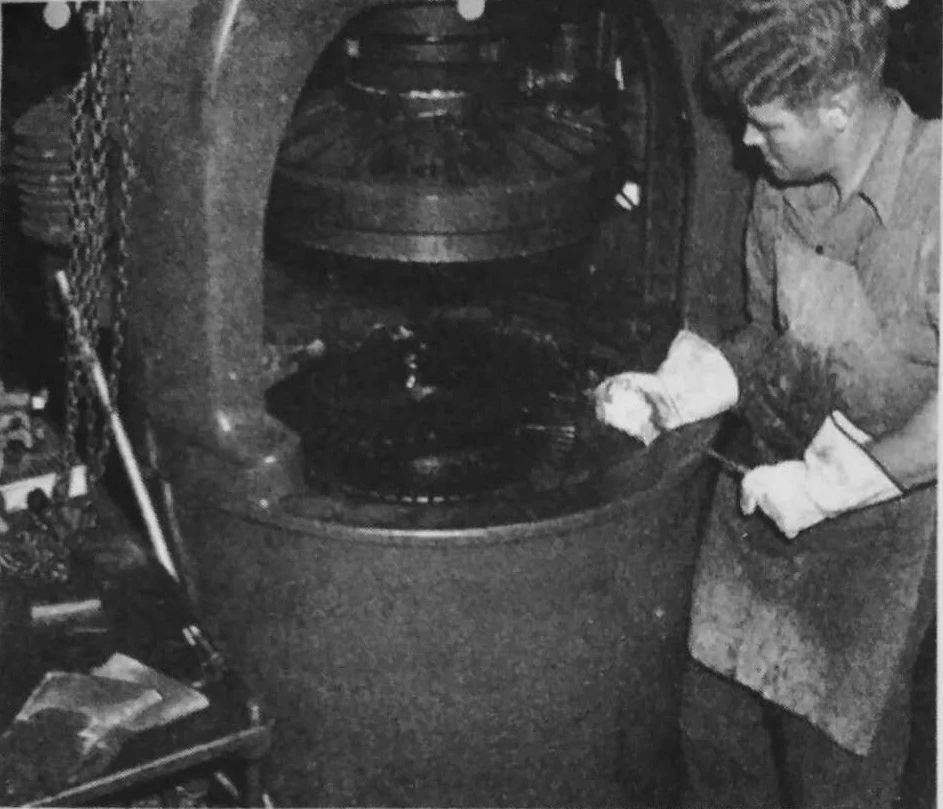
▲图1 一台64cm (25in ) 的自动淬火机床
注:由纽约罗彻斯特格利森(Gleason) 工厂于1930年代早期制造。操作人员正在将一个完成淬火
操作的大型螺旋锥齿轮从下模总成上取下。
这些机器可以由液压或气动(取决于具体设计)系统驱动,能够使用各种各样的淬火冷却介质,最常见的是油。自最初发明以来,虽然这些机器的几何设计和可选特性在过去几十年里有了显著的变化,但它们的基本功能保持不变。现代淬火机床的一种具有代表性的形式如图2 所示。
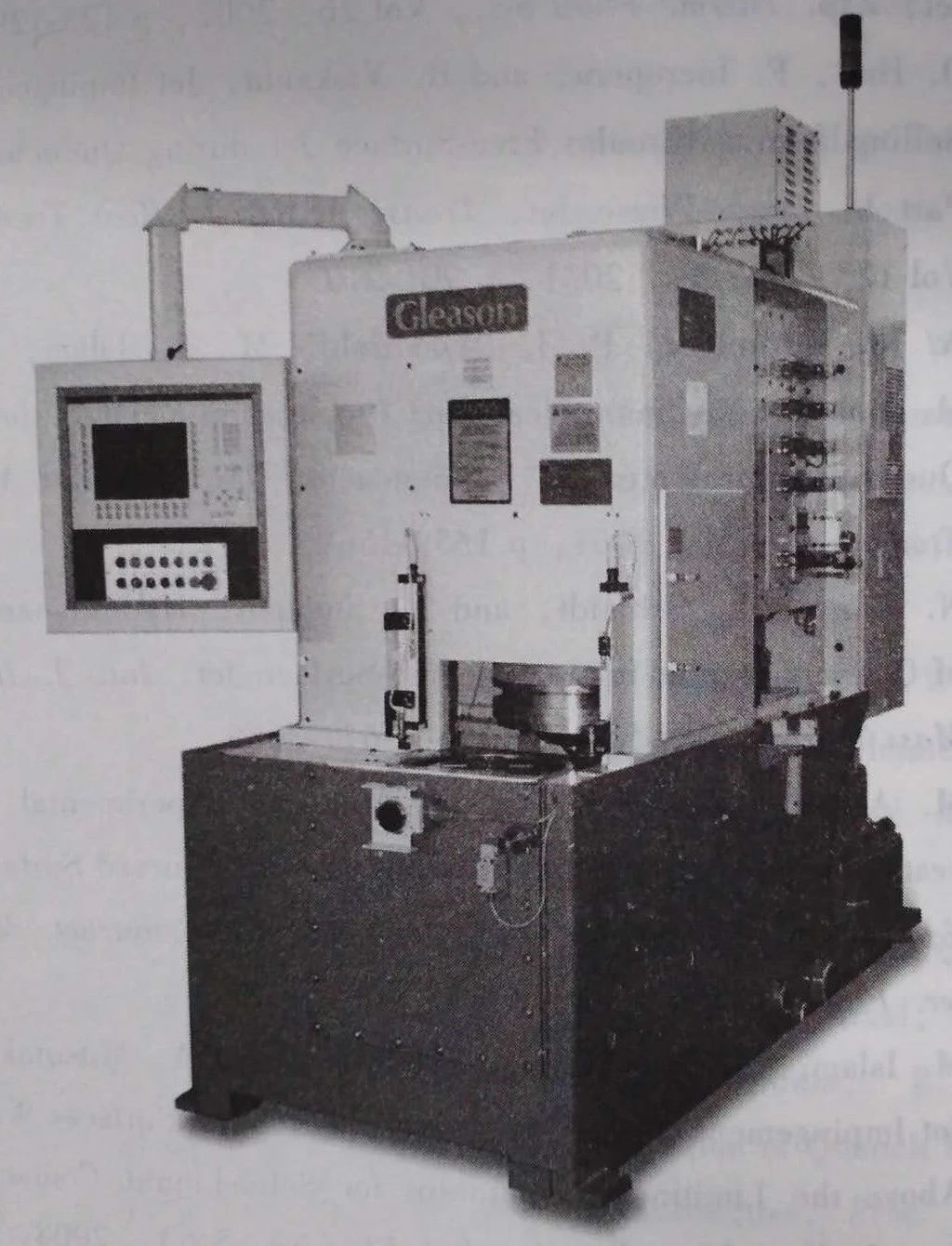
▲图2 Gleason529淬火机床的现代形式
总体设计由一些基础组件构成,包括立式机床部分、一个控制面板、一个下模台、工装和底座。冷却装置用于使淬火冷却介质的温度维持在一个特定的狭窄范围内,它可能属于一个独立的机械系统的一部分,或应用于能同时连接多个淬火机床的中央容器中。机床竖立的部分包括上模顶杆、液压系统分路阀箱、液压管路、电磁阀和阀门、电气面板控制箱。控制屏显示了在淬火周期中可能需要调整的各种性能参数,如图3 所示。
底座既可作为淬火冷却介质的蓄油池,也可支承下模总成,其原理图如图4 所示。
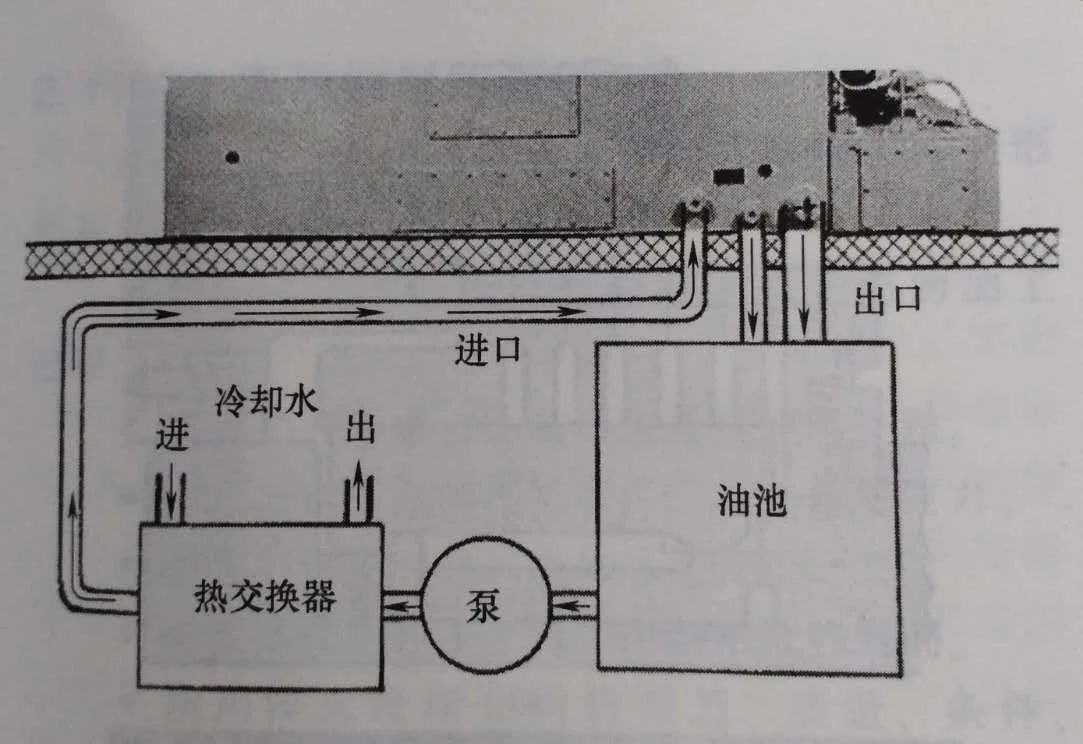
▲图4 油流从油池到冷却装置然后返回淬火机床
立式机身是从机器底座的前面镶嵌进去的,允许在下模中完全存取工件,包括将工件放置在工装上淬火,以及淬火完成后在机器处于“取件”状态时取出工件。
操作时,手动或自动地从一台独立的加热炉(通常是箱体炉、连续转体式炉或推杆炉)中移出淬火工件,放置到下模总成的工装上。下模总成的全貌如图5 所示。
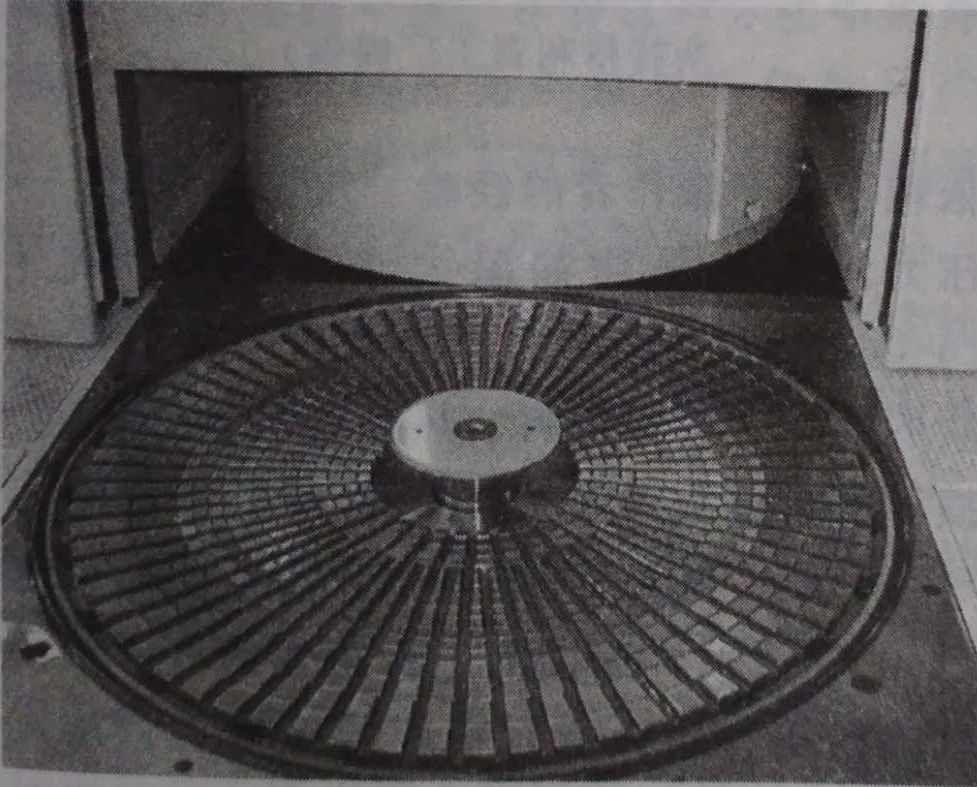
▲图5 “取件”状态下淬火机床的下模总成
注意:弹簧加压的中心扩张器锥体和独立的开槽环
需要注意的是,从加热炉到淬火机床的运输设备的效率通常是压力淬火时的关键参数。转移时间应保持最小值,以使热量损失最少。如果这一步需要的时间太长,那么延迟淬火的结果可能会产生与硬度相关的问题和不希望出现的转变产物。工件成功放置在下模总成上后,机床开始运转,零件缩回上部液压顶杆总成下面的中心位置。机床外部的防护装置随着总成的下降而降低,中间顶杆驱动一个(或多个)内扩张器在指定的压力点与工件内径接触,以保持这些位置的圆度(图
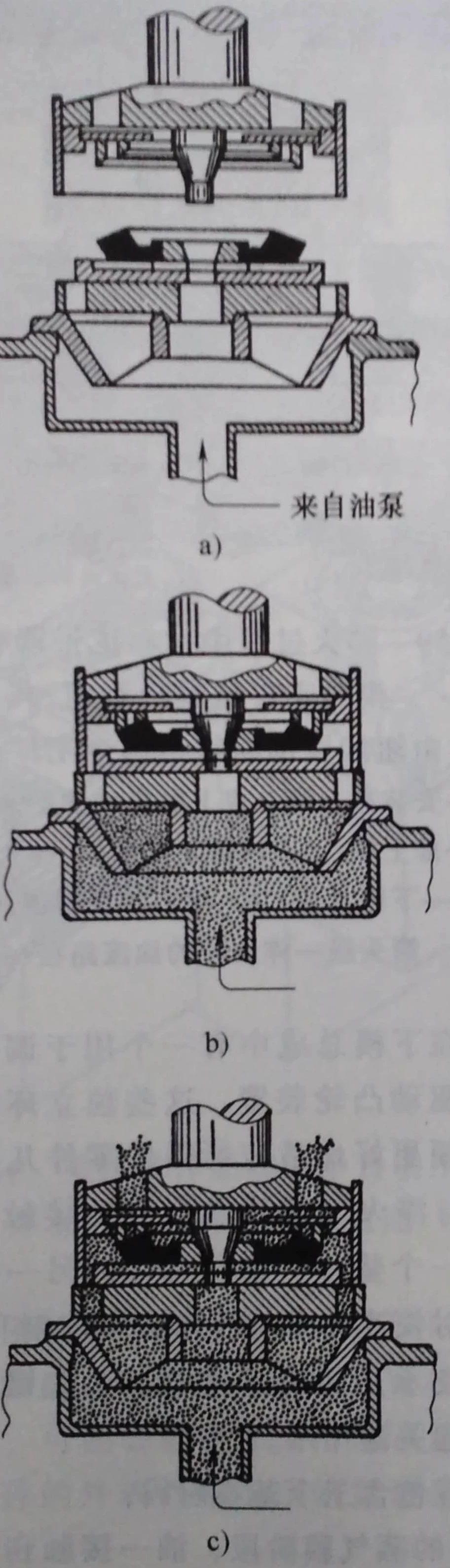
▲图6 压力淬火过程
a) 一个热齿轮被放在下模总成上准备加压淬火
b) 中心顶杆和上部内外模下降与零件接触
c) 开始定时周期,油流开始进入淬火室和零件周围
顶杆总成的每个组件(中心扩张器、内外模)由三个独立的比例阀分别进行控制,且都是通过压力传感器进行监测控制的。在整个淬火周期中,预设的压力水平通常是由扩张器保持的,在某些具有编程功能的机床中,这个压力水平在淬火周期的进程中可以发生变化。在淬火过程中可以降低内外模,使其与淬火工件的上表面相接触,以控制定位、碟形和零件平面度。淬火油的流动是可以预设和预先编辑的,然后在工件淬火时进行激活。
图7 所示为在淬火室中建立的淬火油循环路径的例子。
淬火油通过下模外径周围的开口泵送到淬火室中。随着工件周围的腔室被填满,淬火油流出顶部。如果工装设计合适,则可以通过调整淬火油溢出工件的方向来获得最好的整体效果。可以调整出口处延伸的开口来约束淬火油的流动,或者完全打开以获得最大流量,这取决于零件的需求。下模是由一些不同的带槽的同心圆环构成
的,可以通过旋转获得最大流量,或者约束流向零件底部的淬火油。在淬火过程中,精确地调整这些特性有助于使由散热不均匀引起的畸变最小化。在淬火周期中,也可以通过定时分段来改变淬火油的流速和持续时间,以便为具体的零件建立定义明确的淬火工艺。
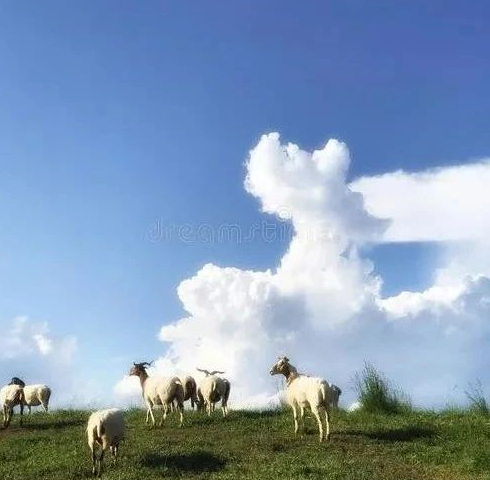
下模台通常装在杆的横截面上,由液压或气动活塞驱动。在下模总成中有一个用于调整独立环的凸轮。通过驱动凸轮装置,这些独立环将会呈现碟形或锥形以便更好地适应所需的零件几何结构(见图8 ) 。为与淬火工件建立合适的接触,每个环的下面需要有一个垫片,这种结构的另一个好处是可以以一种相对快速和简单的方法来切割和安装垫片。零件的合适支承是压力淬火的一个关键方面,模具设计在其中起关键作用。
1) 最初的蒸气膜阶段,油一接触到零件就立即气化,形成一层环绕零件的蒸气屏障,充当一个有效的隔热层。
2) 蒸气传输阶段,淬火油穿过蒸气层,传热速度更快。
为了保证在淬火的初始阶段均匀地散热,淬火冷却介质的流动速度必须足以防止蒸气膜形成。如果在工件表面的周围区域形成气泡,则散热的不均匀性将导致不能接受的硬度变化和变形。当初始淬火阶段成功消除之后,就可以降低淬火冷却介质的流动速度。必须仔细地选择为零件制定的淬火冷却介质的最终流动速度分布,以便满足硬度和几何形状的需求。淬火冷却速率过慢会导致延迟淬火、 硬度变化和不希望出现的转变产物;淬火冷却速率过快,则会造成零件变形和/或开裂。制定合适的淬火冷却介质流动速度和选择淬火冷却介质在零件周围的流动路径通常需要经过反复的试验。淬火的成功通常依赖于机器操作者的经验、知识和技术。
压力淬火的平均油温大多为25~75℃ (75-165°F) , 这取决于淬火操作的本质、使用的淬火冷却介质的类型、零件材料、热处理后的性能要求等。避免损坏盛放淬火冷却介质的机器的密封圈的一项措施是,一般应避免淬火冷却介质的平均温度过
60℃ (140°F)。对淬火油浴进行适当的日常维护很重要,但这在压力淬火过程中经常被忽视,从而导致在这类系统中处理的材料的硬化产生不可预料的变化。随着淬火冷却介质的持续使用,油添加剂逐渐分解,即使连续不断地过滤淬火冷却介质,细小的微粒仍会随着时间的延长而积累。如果未被发现,这将导致淬火冷却速率加快,进而危害油淬过程的完整性。应根据使用情况定期监测淬火槽中淬火冷却介质的黏度、闪点、含水量、沉淀物和沉淀值。淬火冷却介质的测试至少应每季度进行一次。
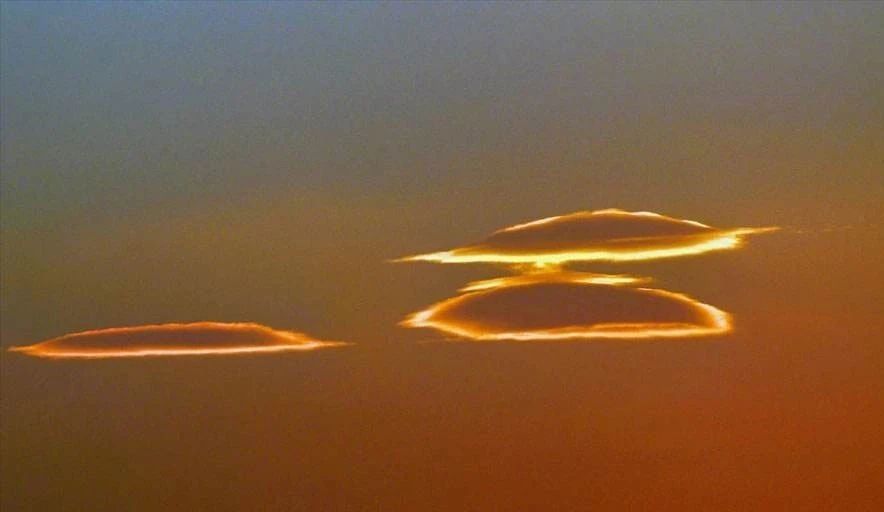
2 变形控制因素
总的来说,在压力淬火操作时,影响工件变形的基本关键因素有:
1)工件的材料的质量和之前的加工过程。
2)工件的残余应力分布和预备热处理过程。
3)淬火操作引起的不平衡热应力和相变应力。
4)使用的钢种和奥氏体化温度分布。
5)奥氏体化炉和淬火机床之间的转移时间。
6)所用淬火冷却介质的类型、质量、条件、温度。
7)淬火冷却介质流过工件时的方向和选择性计量。
8)不同流速的淬火持续时间。
9)适当的淬火模具工装的设计、安装和维护。
10)工件上加压点的位置。
11)为保持工件几何结构所施加压力的大小。
12)脉冲。
上述最后一项是只有压力淬火才有的特性。在淬火时,为了使变形最小化,内外模通常受到脉冲以保持零件的几何结构。脉冲特性周期性地缓和由内外模所施加的压力,在仍保持要求的零件几何形状的前提下,允许组件随着冷却而正常收缩。没有这个特性,模具之间的摩擦接触将会产生应力,零件将不允许组件随着冷却而收缩。脉冲方式有效地减少了这种摩擦接触,避免了由偏心和不平整造成的变形问题。正确实施脉冲技术时,在整个淬火周期中,在保持模具与零件接触的同时释放压力,然后每隔约2s再实施一次。尽管这种方法中内外模是循环的,但扩张器的压力一般并不作脉冲。如今工业中使用的大多数压力淬火机床都采用这种设计特性,然而它并不是最新发展出来的。几十年来,脉冲技术已经成为专为高生产率而设计的半自动压力淬火机床的一个组成要素。这些半自动机床中的一个示例如图9 所示。
每个压力淬火工件都要求对应一个特定的模具工装设计结构和机床设置。在轴承套圈和齿轮中,经常通过扩张分段模具来保持孔径尺寸和圆度。如果工件的孔径非常小而不能承受这些分段模具的话,可以使用一个固体塞作为替代来控制孔的直径和锥度。这个塞子会在淬火之后被压出。重要的是,当下模总成中有不同的定位面时,这些定位面之间的尺寸需要维持在一个小的公差。如果不遵循这一规则,则会产生相悖的结果和不希望出现的变形。除了扩大模具外,收缩模具也可以有效地保持外径的几何公差,这是一个关键因素。齿轮就是一个很好的例子,其薄的辐板部分与相对较厚的轮齿、凸台和轴承直径相连。航天应用中的齿轮经常包含几种这样的特性,可能会造成淬火中的不均衡收缩。可以通过在组件的外表面施加压缩负荷来有效地解决这个问题。
压力淬火时的误差可能是很大的。例如,Φ230mm (Φ9in ) 齿轮上的孔径在未淬硬状态下的圆度误差为0.025mm (0.001in ) , 压力淬火后通常可达到0.064mm (0.0025in )。同样的齿轮,当放置在平板上时,在平板与齿轮表面之间的任意位置均不允许出现0.05mm (0.002in. ) 塞尺可以通过的间隙。对Φ460mm (Φ18in ) 的齿轮,这一间隙应小于0.075mm (0.003in ) 。如果上述所列因素均得到妥善处理(即使用高质量的锻件,加工前正确地进行正火,使用锋利的刀具,遵循良好的加工操作等), 通过压力淬火通常可以达到这种严格的误差要求。压力淬火的一个延伸是使用辊式淬火法控制长1020mm(40in ) 的Φ200mm (Φ8in. ) 的长圆柱形零件、轴、曲轴的变形。这种技术是使用滚轴在热工件上小心地施加可控载荷,此时热工件绕其轴线旋转,而淬火室内充满了流动的淬火冷却介质。图10 所示,为这种高度专业化的淬火机床的一个典型图片。
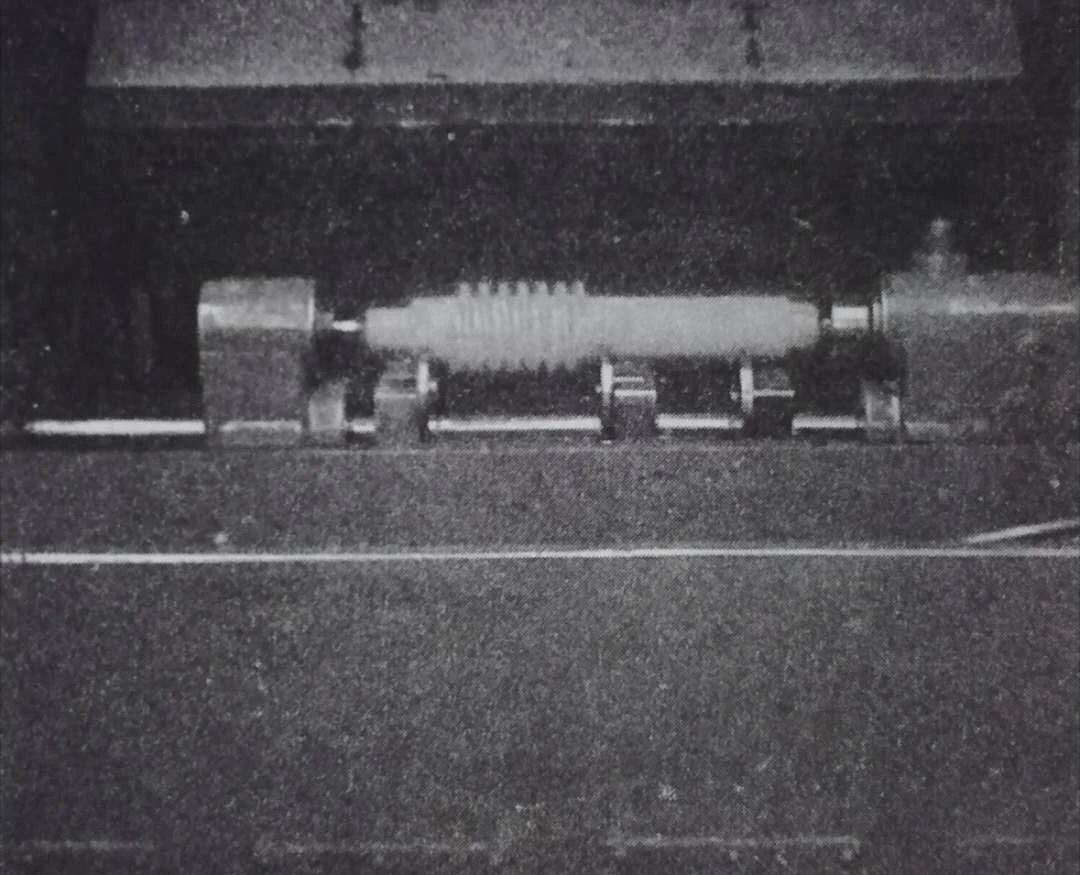
▲图10 压入辊模淬火机床的蜗杆图
如果您对我们感兴趣,请登录网站https://www.hnhta.org.cn/